Uniserve's Eco-Friendly Warehouse Solutions
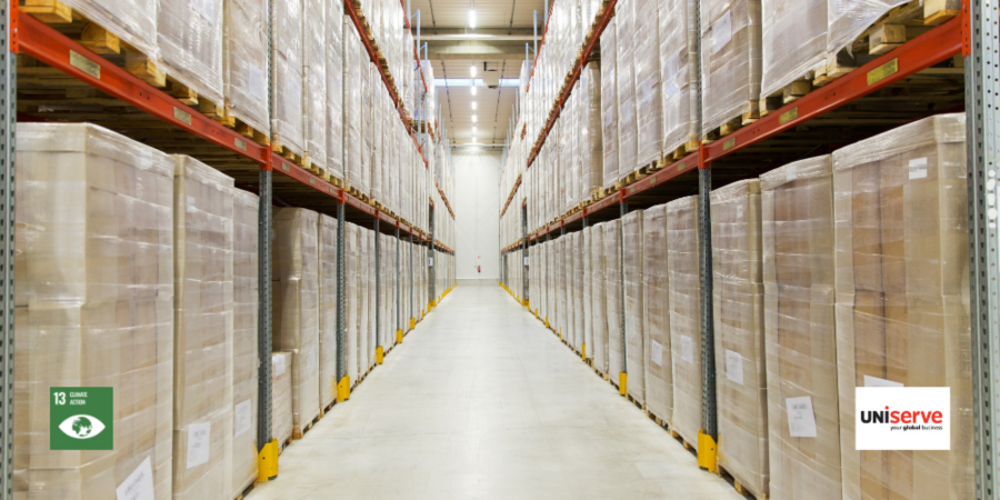
As a Crown Commercial Services (CCS) Supplier, Uniserve Group has committed to Net Zero emissions by 2050 and has entered the Race to Zero. However, sustainability initiatives are not limited to emissions reduction. Uniserve’s Felixstowe Mega Distribution Centre has reduced the plastic waste it produces and also created a safer working environment by introducing a robotic shrink wrap machine to the operation.
The robot navigates autonomously around pallets to wrap them with shrink wrap and can be moved into any area of the warehouse. The technology eliminates the need for manual wrapping, reducing manual handling injuries, and limits the need to move pallets around the warehouse. The resulting reduction in warehouse traffic benefits site safety by reducing incidence of collisions.
The initiative has resulted in lower plastic usage and enhanced safety due to consistent tension application during wrapping, reducing the likelihood of pallet collapses.
The robot ensures efficiency through consistently using the same amount of wrap and creating 300% tension by pre-stretching the wrap before application. A formal study was conducted prior to implementation comparing different types of wrap, leading to the selection of the thinnest wrap appropriate for the goods stored, and ensuring minimal plastic usage while maintaining product integrity. Additionally, the robot has contributed to minimising damages by tightly wrapping pallets immediately upon receipt, preventing pallet collapses even when leaning or partially collapsed pallets arrive at the site. This contrasts with the risk posed by static wrappers, where the spinning turntable can cause stock to fall over, requiring a worker's presence and posing safety risks.
Operating space requirements for the robot can be a challenge, but the alternative static wrap machines or manual wrapping are less efficient and less safe. Planning the workspace effectively is crucial. Training workers on the robot’s need for space and its numerous safety features, such as automatic stopping when it encounters an obstacle, ensured a smooth integration into the workflow.
Use of these robots has resulted in benefits including improved quality, ease of use, and consistency of wrapping. By reducing the amount of plastic used to wrap pallets, the robotic solution has provided environmental benefits and cost savings.
By limiting warehouse traffic and preventing pallet collapses, the solution has enhanced operational efficiency and safety.
- Author
- Uniserve
- Date
- 29/04/2025