TT Talk: How to improve loading dock safety
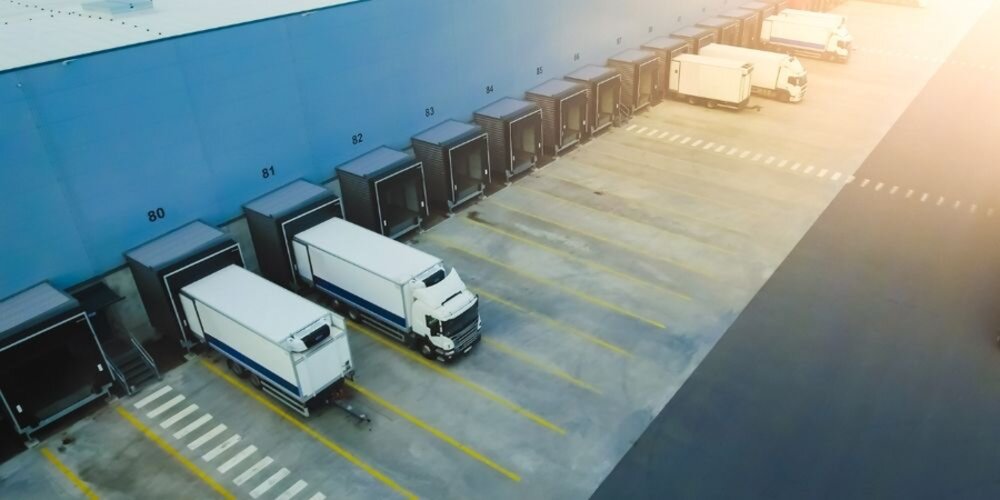
Loading docks in warehouses and terminals are high-risk environments where people, vehicles and cargo come into close contact. Without strict safety measures, accidents in loading docks can result in serious injuries to workers, costly damage to cargo and equipment, and severe operational disruption. This article outlines the practical steps which warehouse and terminal operators can take to reduce the risks.
Preventing collapsing cargo at loading docks
Cargo falling from height either inside or from trailers, containers, rigid trucks and vans is a major hazard in loading docks.
The risk during loading a vehicle can be reduced by using proper lashings and bracing to stabilise the loaded cargo, especially items with a high centre of gravity, and by avoiding stacking heavy goods on top of lighter ones. All handling instructions, such as ‘this side up’, should be followed, and all loaded cargo should be blocked and secured. Operators should train and encourage their workers to spot and report unsafe loading conditions.
The risk during unloading can be reduced by operators working closely with suppliers, hauliers and third-party logistics providers to ensure that similar proper cargo restraint best practices are followed, which in turn will avoid cargo shifting in vehicles before they arrive. In addition, a securing strap may be placed loosely around the handles of the trailer or container doors, enabling partial opening of the doors to check whether the load has shifted..
Stopping people falling from loading docks
Operators with raised loading docks should provide fall-from-height protection and guidance for all workers. This can be achieved by keeping dock doors closed until a vehicle is fully parked; installing chains or physical barriers across open dock entrances when not in use; using visual warnings and signs to alert workers to fall hazards; and providing fall-protection equipment and training.
When loading and unloading double-deck trailers, it is vital to ensure that all safety gates are properly secured before any worker accesses the upper deck. When repositioning or restraining cargo from the edges of curtain-sided trailers, workers and drivers should use fixed or mobile platforms to provide safe access to the trailer bed.
Managing trailer stability with best practice
Uneven loading can cause an uncoupled trailer or container chassis to tip forward over its landing legs. To avoid this potentially serious hazard, the weight and distribution of cargo should be assessed before loading begins. If there is a risk of tipping, a trestle or trailer stand should be placed under the front end.
Furthermore, operators should ensure clear communication between site workers and drivers about load characteristics. Operators should also include stability checks of uncoupled trailers and container chassis in their standard operating procedures.
Stopping unplanned pull-offs with vehicle controls
One of the most dangerous incidents on a loading dock is the unplanned departure of a vehicle during loading or unloading. This can result in catastrophic injuries, especially when mechanical handling equipment such as forklifts are in use.
Unplanned pull-offs can be prevented by confiscating the vehicle keys and clipping them to the loading dock door or placing them in a lockbox. Sites should be aware that drivers often carry multiple sets of keys with the intent to bypass such restrictions. Other vehicle immobilisation methods include using Suzie or kingpin locks to prevent trucks coupling with a waiting trailer or container chassis; installing a red-green traffic light system to show when it is safe to move; and employing mechanical wheel chocks or an automated restraint system.
Operators should produce a written vehicle immobilisation procedure, which all drivers and warehouse workers must understand and follow before loading begins. Also, to ensure drivers leave their cabs during the loading process, they should be provided with a safe and comfortable place to wait. Check too that they always hand over all sets of keys.
Using dock doors and levellers safely and efficiently
Finally, malfunctioning loading dock doors and levellers can lead to accidents, delays and costly repairs. It is therefore important to conduct regular inspections of dock doors for wear, damage or misalignment, and to ensure routine dock leveller maintenance in line with manufacturers’ guidelines – including checking all hydraulic systems for leaks.
Operators should train and encourage workers to report door and leveller faults at once, and to tag defective equipment until it is repaired. Maintenance logs should also be kept to track service intervals and repairs. It should be noted that mechanical dock levellers are considered lifting equipment and should be periodically inspected as such in accordance with local regulations. In addition, work teams should be trained to perform pre-use checks of all dock mechanical equipment—including dock doors and dock levellers—at the start of every shift.
Conclusion
Loading dock accidents can cause serious injuries, cargo damage and disruption. By addressing the most common hazards of cargo falls, people falls, trailer tipping, unplanned vehicle pull-offs and dock equipment failure, warehouse and terminal operators can significantly reduce the risk of such incidents. A culture of safety, reinforced by training, clear loading dock safety protocols and well-maintained infrastructure, will reduce injury risk and improve operational continuity in these high-risk zones.
- Author
- Josh Finch
- Date
- 01/07/2025