TT Talk - Why automated warehouses are safer places to work
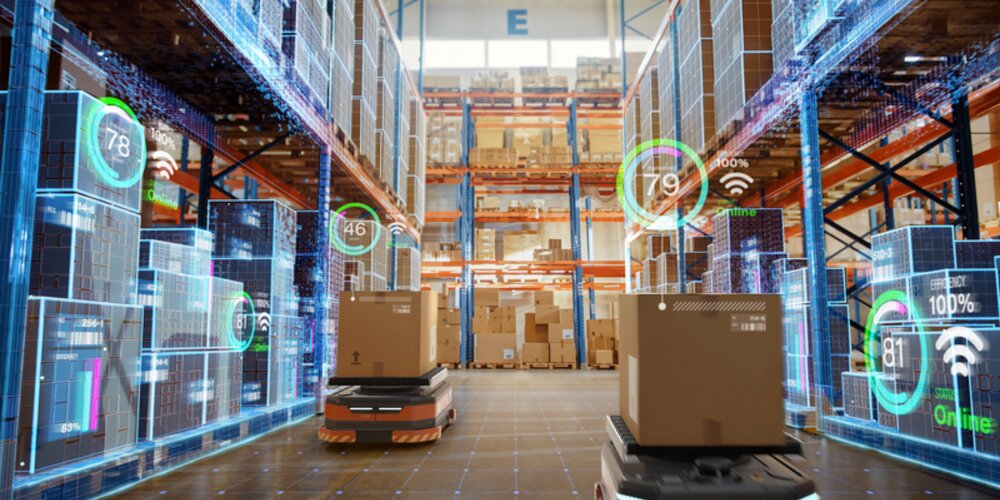
Warehouse automation increases efficiency, reduces costs, raises productivity and – most importantly – improves worker safety. This article focuses on the various safety benefits of warehouse automation, including enhanced safety measures, real-time hazard detection, improved training and compliance, and reduced exposure to hazardous conditions.
Traditional warehouses can be dangerous places to work. The US Bureau of Labor Statistics reported in 2021 that the rate of injuries and illnesses in warehousing was more than double the national rate across all industries. Improving worker safety is a key outcome that is driving the transport and logistics industry towards greater automation of warehouses globally. According to a 2023 report by McKinsey & Company, warehouse automation is growing by more than 10% annually. Interact Analysis estimated in 2023 that more than a quarter (26%) of the world’s warehouses will be automated by 2027, up from 14% just a decade earlier.
DHL, which embraces automation through their ‘smart warehouse’ initiatives states that; “automated processes provide a greater degree of elasticity to logistics infrastructure. Warehouse employees benefit from improved health and safety conditions while also being spared the most repetitive and strenuous tasks”.
Warehouse employees benefit from improved health and safety conditions while also being spared the most repetitive and strenuous tasks
Enhanced safety measures
Warehouse automation refers to the use of technology and automated systems to perform tasks traditionally carried out by human workers in a warehouse setting. This can include everything from automated mobile robots (AMRs) and robotic arms to sophisticated software systems that manage large scale storage and retrieval systems (ASRS).
One of the greatest potential benefits of warehouse automation is the reduction in workplace accidents and injuries. Automated systems can handle tasks that are hazardous to the workforce, such as lifting heavy or awkward objects, working at height or being in extreme temperatures. By automating these tasks, automated systems can significantly reduce the risk of accidents and injuries.
For example, AMRs can be used to transport heavy loads across the warehouse floor without the need for people. This reduces the risk of workers suffering from musculoskeletal injuries due to heavy lifting. Similarly, robotic arms can perform repetitive tasks with precision, reducing the likelihood of human error and associated risks. Automated storage systems eliminate the need for reach trucks and the associated risk of collisions and pallets dropped from height.
Automated systems reduce the number of times goods must be handled, freeing up worker’s time as well as equipment for other tasks. For example, Perpetual Inventory (PI) cycle counts are traditionally carried out using a forklift or reach truck to audit storage locations. Robotic inventory management systems now carry out this task, freeing up trucks to complete other work. Many ASRS systems are able to self-audit inventory stores, providing even greater improvements to efficiency while minimising the risk of damage to stored goods by reducing the number of times that goods are handled during storage.
Automated warehouses enhance safety; however, maintaining cargo cover for freight forwarders remains essential.
Real-time hazard detection
Automated safety systems use advanced technologies and intelligent algorithms to check and control safety processes within warehouses. These systems can have a range of features, including real-time monitoring, hazard detection and emergency response. By integrating automation into their safety protocols, warehouses can significantly improve the overall safety and well-being of their workers.
By integrating automation into their safety protocols, warehouses can significantly improve the overall safety and well-being of their workers
One of the key benefits of automated safety systems is the ability to detect and respond to potential hazards in real-time. Using sensors and smart algorithms, these systems can spot risks such as unauthorised access, collisions or equipment malfunctions. Once a hazard is detected, the system can automatically trigger alarms, notifications or even take corrective actions to prevent accidents. This active approach to safety minimises the reliance on people and reduces the chances of accidents or injuries.
Warehouse automation can also contribute to improved training and compliance with safety regulations. Automated systems can be programmed to follow strict safety protocols and ensure that all tasks are performed to industry standards. This reduces the risk of human error and ensures that safety measures are consistently applied.
Reduced exposure to hazardous conditions
Another significant safety benefit of warehouse automation is reducing workers' exposure to hazardous conditions. Automated systems can handle tasks that involve exposure to harmful substances, extreme temperatures or other hazardous environments. This minimises the risk of workers suffering from health issues related to these conditions.
For instance, automated systems can be used to handle hazardous materials, such as chemicals or flammable substances, reducing the risk of spills or accidents. Similarly, they can work in environments with extreme temperatures, such as cold storage facilities, without putting workers’ safety at risk. This not only improves safety but also enhances overall productivity by allowing operations to continue without interruption.
Safety through efficiency and productivity
Warehouse automation also increases efficiency and productivity, and these benefits directly improve safety too. When workers are not burdened with physically demanding or dangerous tasks, they can focus on more value-added activities. For example, warehouse robots that implement a cluster solution bring picked goods to a warehouse operative in charge of a picking zone, removing manual handling and much of the tedious activity that picking traditionally requires. The operative is freed to focus on the organisation of the zone and achievability of pick targets. The work is less strenuous and more engaging, leading to a decrease in manual handling injuries as well as an increase in warehouse productivity.
Automation presents new opportunities and challenges for logistics operators, making transport insurance more essential than ever.
Conclusion
Warehouse automation offers many benefits, with enhanced safety being the most significant. By reducing the risk of accidents and injuries, improving training and compliance, and minimising exposure to hazardous conditions, automated systems create a safer and more efficient working environment.
As businesses continue to adopt automation technologies, the safety and well-being of workers should remain a top priority, leading to a more productive and sustainable future for the transport and logistics industry.
-
If you would like further information, or have any comments, please email us, or take this opportunity to forward to any others who you may feel would be interested.
Documents
TT_Talk_-_Edition_321__Chinese_.pdf (580 kB) 21/08/2025
- Author
- Neil Dalus
- Date
- 07/04/2025