TT Talk - Mitigating the corrosion nightmare
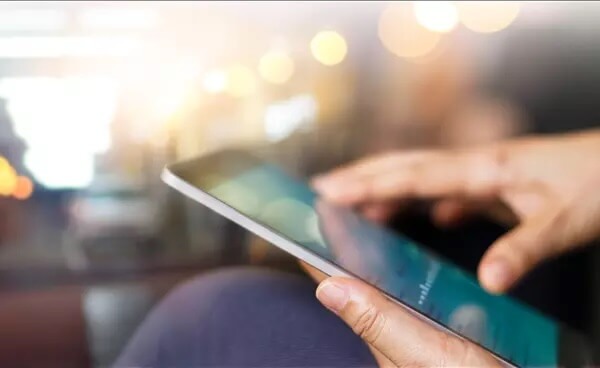
Corrosion is a perennial concern for tank container owners and operators. The stainless steel construction is resistant to staining and corrosion, but may be vulnerable to pitting from certain cargoes or certain cleaning and maintenance operations. Visually minor pitting may conceal development of substantial or even catastrophic corrosion below the surface.
It may be expected that UN Class 8 dangerous cargoes (Corrosive Substances) are the predominant challenge where corrosion of UN portable tanks (tank containers) is concerned, although such commodities are not alone in presenting risk. In terms of classification however, corrosive substances are tested against a criteria of causing severe damage when in contact with living tissue and in the event of leakage are capable of damaging or destroying other goods, or means of transport.
For the purposes of classification under the IMDG Code, substances identified in Packing Groups I and II are not tested against their corrosivity towards the stainless steel shell of the tank container, but against the destruction of intact skin. Substances assigned to Packing Group III demonstrate corrosion whereby it either causes damage to living tissue to full skin thickness, or exhibits a corrosion rate on either steel or aluminium surfaces exceeding 6.25mm per year at a test temperature of 55DegC when tested on both materials.
It is clear from the provisions of the IMDG Code that if tests are conducted on substances considered to be corrosive that cause destruction of living tissue to full thickness, there is no requirement to determine the effect those substances may have on steel. Thus, tank container owners or operators need further information to determine if a corrosive substance is harmful to their asset.
"tank container owners or operators need further information to determine if a corrosive substance is harmful to their asset"
Predominantly, the tank vessel is constructed of stainless steel, which resists many mineral acids, such as nitric acid and concentrated sulphuric acid. It has an excellent general corrosion resistance against a wide range of chemicals that would otherwise corrode normal carbon steel.
It is the chromium content within the stainless steel that forms a protective, complex oxide layer; it is only a few atoms thick and this alone resists corrosion. It should be highlighted however that this passive layer can be susceptible to damage and attack.
There are six primary types of corrosion affecting stainless steel:
- Pitting corrosion - local disruption of the passive layer
- Crevice corrosion - local corrosion caused by reduced oxygen to the surface (such as bolted connections)
- General corrosion/ attack - aggressive chemical corrosion
- Stress corrosion cracking - tensile stress, temperature and corrosive species
- Intergranular corrosion - sensitisation (not usually relevant to low carbon stainless steel)
- Galvanic corrosion - dissimilar metal corrosion
How corrosion works
Once the passive layer is breached, the local area becomes 'active', resulting in the formation of a corrosion cell leading to further damage. This may be caused by exposure to aggressive halide ions (chloride and fluoride), contamination, physical damage, low oxygen environments or under-deposit corrosion.
It should be noted that in an oxygen rich environment, in the absence of pitting, the passive layer can self-repair.
Pitting is most commonly caused through contamination and the presence of halides (such as chlorides). The greater the PREN1 , the more resistant to halides the stainless steel will be. However, after long periods of exposure to cleaning regimes, aggressive chemicals, sediments and the general rigours of transport, the stainless-steel of tank container units will become depleted of the beneficial chromium at the surface resulting in decreased passivity.
Taking action
Operators should focus on having their equipment cleaned as early as practicably possible following transport. Some cargoes can change in composition once humidity and air have been introduced following discharge, which can give rise to an increased corrosion risk.
"Operators should focus on having their equipment cleaned as early as practicably possible following transport"
The passivity is easily monitored and can be restored by passivating (or pickling and passivating) in solutions containing nitric acid. If the surface has become pitted over time, then this often needs to be mechanically removed by grinding as the geometry of pits can limit oxygen at the surface, making passivation difficult.
Brookes Bell is currently developing ground-breaking 'eddy current array sensors' for stainless steel in conjunction with Eddyfi. This seeks to provide a cost effective and efficient means of identifying the extent of damage in the tank containers pressure vessel, providing a visual map of areas of damage and, for the first time, identify the depth and shape of pits under the surface.
"The eddy current array sensor technology will enable tank container owners and operators to detect very small pits and cracks over large surfaces at high speed"
The eddy current array sensor technology will enable tank container owners and operators to detect very small pits and cracks over large surfaces at high speed. The technology is able to perform highly accurate depth analysis. The construction of the equipment is such that it is adaptable to operate on any surface contour. It is anticipated that utilising this technology will not only improve the accuracy of current practices, but will vastly reduce inspection time, whilst strengthening the overall repair process. This should give owners and operators greater confidence in the integrity of the metal structures of their tanks.
We gratefully acknowledge the assistance in the preparation of this article of Dr Penelope Cooke, Consultant Scientist, and, Dr Ken Kirby, Consultant Metallurgist, Brookes Bell (a member of the Thomas Miller Group)
We hope that you have found the above interesting. If you would like further information, or have any comments, please email us, or take this opportunity to forward to any colleagues who you may feel would be interested.
We look forward to hearing from you.
Peregrine Storrs-Fox
Risk Management Director, TT Club
1PREN (Pitting Resistance Equivalent Number) of a particular grade of stainless steel is an arbitrary scale for determining how effective a particular grade of stainless steel is at resisting corrosion, and this can be calculated by knowing the chemical composition
- Author
- Staff Author
- Date
- 01/10/2019